This is a guest post by Mr. Ian Gray, Managing Director of Sigra Pty Ltd.
Towards a technology for shallow testing in civil projects
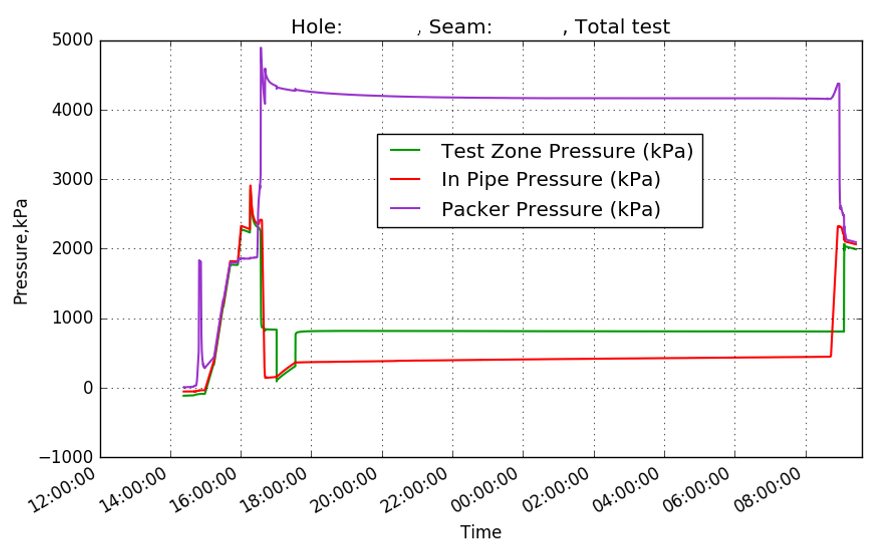
We have found that the equipment and methodology being employed for permeability testing in shallow wells to be, if not inadequate, at the very least misapplied.
We propose a cross-disciplinary approach — involving new technology and the application thereof — to meet the requirements of shallow permeability testing.
Permeability measurement is important because it is part of the prediction of the rate of fluid inflows, fluid loss, or how fluid pressures vary in the ground. For instance, a civil engineer will want to know whether ground water will pose a problem for whatever structure they are designing and building.
Apart from the rare instance of a steady state situation, all formation pressures change with time, and therefore the ability of the ground to store fluid matters.
To sensibly conduct any measurement one must first understand the geology.
While it’s acceptable to gain such an understanding from either borehole samples, borehole geophysics, or broad area methods like seismic or resistivity, we feel it’s much more useful to employ all these methods together.
Each engineering discipline has developed its own way of measuring permeability and storage behaviour, and we do feel that these practices have often proved inadequate, specifically in reference to civil projects, and could be improved with some understanding of the process and the use of suitable technology.
Let us examine these practices.
Methods and issues encountered by hydrogeologists and petroleum engineers.
Hydrogeologist
The hydrogeologist who requires groundwater will choose to drill a well or wells into a suitable aquifer, and will pump from this to determine the production rate versus pressure (head) depletion in the well.
They will then observe pressure (head) changes in adjacent wells, so that the storage behaviour of the aquifer may be deduced.
These other wells are of course an extra cost to any project. However, they are the only way in which the storage behaviour in the ground may be properly determined.
Long term pumping tests of wells and the response in adjacent wells is a very good way to determine aquifer characteristics. Hydrogeologists will interpret their measurements in terms of hydraulic conductivity, which is a combination of absolute permeability of the ground and the viscosity of water.
They will describe the storage behaviour in terms of yield of fluid per unit area per unit fluid head change. The storage term used for a confined aquifer is storativity, and for the unconfined case, specific yield.
Petroleum Engineer
The petroleum engineer will drill a well which is usually deep and expensive. They wish to test the formation (ground) as quickly as possible because drill rig time is real money.
They seldom use pressure measurements in adjacent wells to determine storage parameters, due to the prohibitive costs of such wells for pressure sensing.
Because of the variation in fluids with location and time, the petroleum engineer focuses on absolute permeability and in determining the fluid parameters, such as viscosity and density, separately. The determination of storage behaviour is as much as possible determined by laboratory studies of core.
The key words regarding storage here are porosity and compressibility (change in porosity) of the rock, and compressibility of the fluids. They are a function of fluid pressure.
The hydrogeologist and the petroleum reservoir engineer both want to know permeability and storage. In addition, the hydrogeologist will probably want to know something about the recharge mechanism of groundwater. Any field testing undertaken by either of these disciplines will focus on examining transient behaviour.
The hydrogeologist will usually want to pump at a constant rate until the transient behaviour of the well can be defined, while the petroleum engineer will frequently use a drill stem test (DST) to produce fluid for a short period, then shut in the production zone and wait until the transient recovery behaviour is well established.
Both disciplines will want to obtain information on their reservoir or aquifer away from the test well. This is accomplished by the use of pressure measurement in surrounding wells, or by suitably designed test methods and analysis.
Permeability testing methods used in Civil Engineering and the issues they encounter.
The civil engineer, and to some degree the mining engineer, want to know whether water will be a problem for whatever structure they are designing and building. Their concern then is likely to be water make into an excavation, tunnel or mine, water loss from a dam or through an embankment.
Very frequently they wish to know what the pressure distribution is within the ground, as it directly affects the effective stress, and therefore the potential for failure.
Sometimes the civil or mining engineer will employ a full pumping test with associated pressure observation by piezometers. These cases are however unusual. Time and cost pressures have tended to lead to a series of short term tests that have been historically used.
In soils, these are typically falling head or slug tests, in which a hole is filled with water and the rate of change of head and hence volume change within the hole, is monitored for a period.
In rock, the test method is typically the packer test, in which a section of hole is sealed, and water is pumped in at a fixed pressure of one atmosphere as measured at surface, and the rate of inflow is monitored.
The final supposedly steady state (10 minute) flow rate is measured in Lugeons (litres/metre/minute), a value that was developed originally to simply determine whether the ground would take cement grout.
However, neither of these tests can be analysed to produce real values of permeability, and by definition single hole tests cannot provide any information on the storage behaviour of the ground.
Issues associated with the Falling Head Test
The falling head test produces a varying rate inflow.
The problem with this is the difficulty in separating pressure loss around the well bore, usually associated with drilling, from the response of the soil outside the zone of influence of the well.
This problem is made much worse because the process of injection almost invariably carries soil particles into the zone around the well bore, thus changing the near well bore behaviour. This means that it is not generally possible to separate near well bore pressure (head) loss from the transient response in the ground.
The results of such tests are therefore misleading—if the test is left for long enough to come to stabilisation it can yield information on the groundwater fluid level.
Issues associated with the Packer Test
The methodology of the packer test is that it should reach a steady state of fluid injection. If in fact it does so, it is an indication that the pressure drop between the rock and the fluid pressure within the hole are dominated by near well bore losses, typically by the size of the joint openings to and adjacent to the borehole.
The real information from such tests on the rock mass being tested is lost, because no attempt is made to determine the transient response of the ground.
Neither does the test provide information on the fluid pressure (head) within the ground, nor take this into account in how it affects the inflow rate.
Literature abounds on how to interpret such tests, and spurious correlations are published between the value of Lugeons and units of hydraulic conductivity, and by consequence, permeability.
We therefore have two tests that are widely used by the civil engineering industry which cannot provide the information that is required. Indeed, the results obtained are misleading, and their adoption could lead to serious errors in design. What can be done to remedy this?
The short answer is to change test methods.
Adopting the oilfield Drill Stem Test (DST) for civil and mining applications.
The most effective way to do this is to adopt the analogue of the oilfield DST for civil and mining applications. We have used these extensively for the coal seam gas and deep coal mining clients. We developed equipment and analysis to suit these applications.
The test needs a period of flow followed by zero flow from the test zone, during which pressure stabilisation is achieved. This is followed by an inflow period and then a period of no flow from the test zone, during which the pressure buildup is monitored.
This buildup time must be long enough to get a meaningful answer.
Low permeability ground tends to take a lot of time for the pressure recovery to deliver results with a useful measure of permeability. If there is no need to measure permeability down to low levels, then the test may be terminated early without providing precise value.
While flow from the test zone is the best choice, as it avoids contamination of the well bore with foreign fluids and clay particles, it is sometimes more practical to inject for a period at a constant rate, or by falling head, in the drill string. Changing the flow direction does not change the basis of analysis.
In Soil
These test techniques may be applied to soils, where the test may be conducted through a casing or standpipe, with the use of a downhole packer and pressure transducer to control flow. In rock, the equipment required to conduct a test comprises a single or straddle packer system, which incorporates a valve to control flow from the test zone.
Flow from the test zone is facilitated by purging the drill string of fluid prior to the test, or by running the tool into the hole with an empty drill string so that flow may occur into the drill string.
Pressures in the test zone need to be accurately logged, something that is relatively easy with the range of transducers and logging devices available.
Such tests can yield accurate information on permeability, and such features as barriers to flow or recharge boundaries within the ground. What they cannot do is provide information on the storage characteristics or the anisotropic nature of permeability.
To achieve this, other pressure sensing points (piezometers) must be installed.
This brings the testing process full circle, to one where a full pumping test might be used with at least three correctly placed piezometers to enable the determination of anisotropy in permeability and the storage behaviour.
The problem with this approach is that it is not possible to differentiate between anisotropy and inhomogeneity.
There is an alternative that enables the measurement of both inhomogeneity and anisotropy: Pulsed DST.
This involves sequentially testing individual boreholes and placing piezometers in these as each borehole test is finished. The next borehole to be tested sends a pressure transient to those boreholes drilled before and fitted with piezometers. The most convenient way to test each well is by conducting a DST in the test zones. Hence the name “pulsed DST”.
This method enables multiple measurements of mean permeability and directional permeability, so that both inhomogeneity and anisotropy may be assessed.
Guest Author: Mr. Ian Gray – BE, MAppSc, PhD, RPEQ, MAusIMM, SPE, Managing Director, Sigra Pty Ltd, Brisbane.
Acknowledgement: Geotechpedia team would like to thank Mr. Ian Gray, Sigra Pty Ltd, Managing Director for sharing this post through Geotechpedia.
Disclaimer: Any views or opinions represented in this post are personal and belong solely to the author and all content provided is for informational purposes only. Geotechpedia makes no representations as to the accuracy or completeness of any information on this post or found by following any link on this post.